The table below shows the types of characteristics of the materials used by Katsura for the covering of rubber rollers.
ABOUT ROLLERS
- What is RUBBER ROLLER?
- About Special Surface Finish
What is RUBBER ROLLER?
Rubber roller is “a rubber or an elastic material covering the core made of
metal or other materials”
Rubber rollers are used in wide application, utilizing its
features listed below;
Characteristics of Rubber Rollers
- 01High coefficient of friction
- 02Quickly returns to its original shape when the shape is distorted.
- 03Resistant to chemical substances and protects the roller core and shaft.
- 04Prevents damage caused by scratching and bumping.
- 05Compensates for small changes in machine precision.
- 06It has many special uses;
Roller core
In addition to the rubber quality, the quality of the roller core is also very
import xant for the uses under various conditions.
That is, unsuitable material and structure could cause serious problems.
Generally, steel
tubing is used as a material but for special purposes, materials such as stainless steel,
aluminum and plastic are also being used.
CFRP (Carbon Fiber Reinforced Plastics) cores
are also widely recognized for some special purposes such as a light weight requirement.
(Please refer to our CFRP brochure for more information)
Roller core structures are
different depending on the usage condition. Please consult our sales staffs.
Roller core structure
Representative structures are as follows:
- 1One Flange Type
- 2Integral Type
- 3Two Flange Type
- 4Rotation Type
Roller Balance
As machinery is constantly being improved to make the operation faster, the problems due to the roller unbalance increases. For example, vibration, noise, premature wearing down of the bearings, cores, gears, premature damage of the rubber roller and machinery itself, etc….
These problems arise because of the rapid increase in the centrifugal force due to the unbalance of the roller, as the roller revolution speed increases.
Katsura employs the following methods to adjust the unbalance;
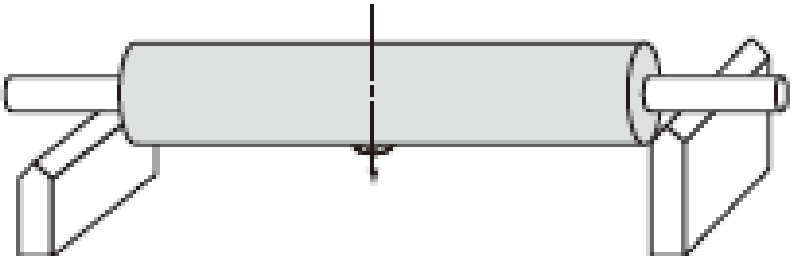
Static Balance
Static balance shows the evenness of load distribution of the roller component. The balance is checked by seeing if the roller moves on the sharp edges as shown in the sketch below. Correction is made by adding weight to the lighter side or lightening the heavier side.
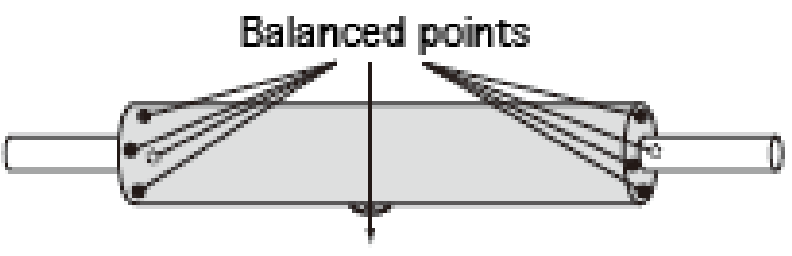
Dynamic Balance
Dynamic Balance is measured to make the roller rotate. The
unbalanced weight is described as centrifugal force which results in the
roller swinging in a certain direction.
To correct the dynamic
balance, the roller surface is divided into 360 equal parts and weight
adjustments are made at the positions where the unbalance is exerted.
- Number of rotations of the roller
- Desired balance weight (g)
Generally
G6.3(Balance Grade) for rollers for film and paper industries (less than 400m / min)
G2.5(Balance Grade) for high revolution rollers (400 - 1500m / min)
Crown processing
Crown height is the difference between the diameter of the roller center and
the diameter of near the roller end (Generally 50 mm from the end)
The purposes of
giving crown to rollers are:
a. Correction of the roller deflection during operation. (Uniform contact)
b. Making the most appropriate flow of the substrate such as cloth, plate and paper. (To avoid meandering)
It is better to give crown especially to the following rollers.
- The value of L/D (roller length / roller diameter) is relatively big.
- The pressure of the roller is relatively big.
Crown types
-
1a. Tapered crown
Application: Conveying roller, Pulley
-
2b. Radial crown (Barrel crown)
Application: Squeezing, Laminating
-
3c. Reverse crown (Concave crown)
Application: Guide roller
Characteristics of each rubber grade
Rubber hardness
Depending on the applications, various rubber hardness is used, from very hard
one like metal to very soft one like sponge.
You can predict the compression strain of
the rubber by the hardness.
The rubber hardness determines the nip width and the contact
time between the substrate and the roller.
Hardness tester
Durometer A (Shore-A) is generally used for soft rubbers. Asker C is used for sponge materials. Durometer D is used for extremely hard materials.
Influence of Temperature on Rubber Hardness
An increase in the temperature usually results in a decrease in the hardness of common types of rubber. Hardness should be compared at the same temperature, accordingly.
The environmental temperature standard under JIS is 23 ± 2 degrees.
The temperature dependency of the hardness of Katsura’s representative materials is shown in the table below.
Temperature (℃) / Material Name |
-10 | 0 | 10 | 20 | 30 | 40 | 50 | 70 | 100 |
---|---|---|---|---|---|---|---|---|---|
White 270 | 84 | 75 | 71 | 70 | 70 | 70 | 70 | 70 | 70 |
White 370 | 82 | 75 | 71 | 70 | 70 | 69 | 69 | 68 | 67 |
White 770 | 75 | 73 | 71 | 70 | 70 | 70 | 70 | 70 | 70 |
White 970 | 70 | 70 | 70 | 70 | 70 | 70 | 70 | 70 | 70 |
White 3370 | 82 | 75 | 72 | 70 | 70 | 70 | 70 | 70 | 70 |
6070 | 85 | 80 | 76 | 70 | 70 | 69 | 69 | 69 | 69 |
7070 | 76 | 74 | 72 | 70 | 70 | 70 | 69 | 69 | 69 |
Black 1370 | 75 | 72 | 71 | 70 | 70 | 70 | 70 | 70 | 70 |
Special surface grooving
Groove cutting and Screw-thread cutting
Rubber rollers with various types of cutting are widely used in various fields. The main purposes of cutting are;
- 01To increase the amount of coating
- 02To smooth out wrinkles in plastic films and papers.
- 03To prevent a belt slipping and meandering
- 04To emboss on plastics.
- 05To assist the heat release from rubber rollers.
- 06To apply softness of rubber rollers.
- 07To raise the coefficient of friction
- 08To improve contact stability with papers or plastic films.
The standard shapes are shown in the diagram below.
Vertical Groove
Single vertical groove
・Purposes : ④, ⑤, ⑥, ⑦
・Applications : Cardboard(Throw-in roller)
Ordering instruction
・Required number of grooves
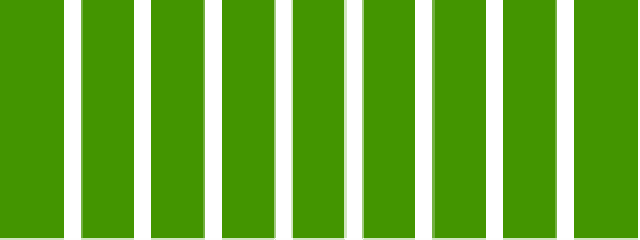
Horizontal groove
Single vertical groove
・Purposes : ④, ⑤, ⑥, ⑦
・Applications : Cardboard(Throw-in roller)
Ordering instruction
・Required number of grooves
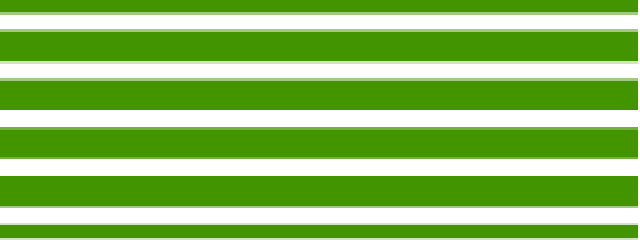
Helical groove
Multi-spiral groove
・Purposes : ③, ⑤
・Applications : Belt sander for plywood, metal plate
Ordering instruction
・Require number of grooves and an angle of the spiral.
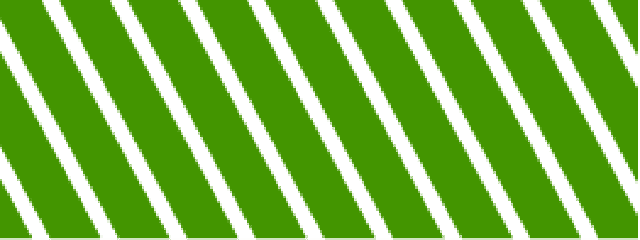
Double helical groove
iral dMulti-spivided at the center
・Purposes : ②, ③, ⑤
・Applications : Belt sander for plywood, metal plate
Ordering instruction
・Require number of grooves and an angle of the spiral.
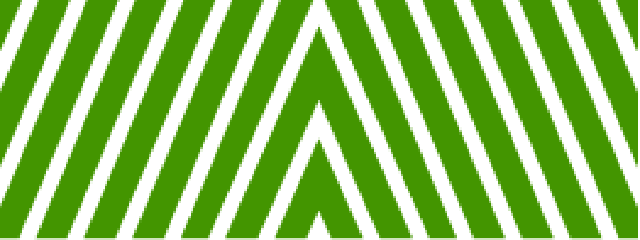
Worm groove
Single line and multi-spiral groove
・Purposes : ②, ③, ⑤
・Applications : Worm rollers for paper manufacturing, dyeing,
guide rollers
Ordering instruction
・Require number of grooves and an angle of the spiral.
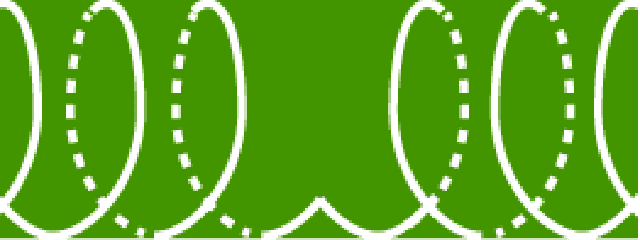
Diamond cut groove
Going & returning multi spiral groove
・Purposes : ③, ⑤, ⑧
・Applications : Grip rollers for cardboard, cloths. Rollers for various kinds of film industry
Ordering instruction
・Require number of grooves and an angle of the spiral.
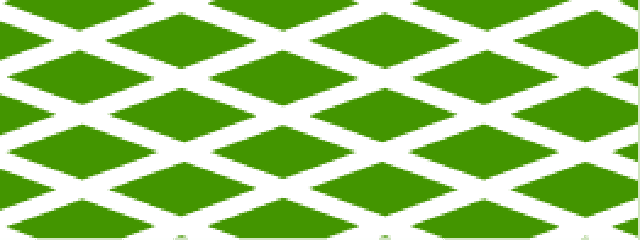
Screw-thread groove
Continuous thread grooves
・Purposes : ①
・Applications : Coating rollers for plywood, metal plate, cardboard
Ordering instruction
・Number of ridges per inch, Direction of thread (right or left)
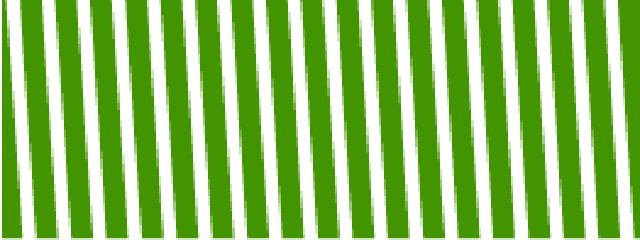
Rubber roller handling
For taking a good care of rubber rollers
Instruction for transport
- Using a solid wooden box is desirable.
- Attach a rope to the shafts or attach a wide belt at the center when lifting a roller. Avoid attaching chains or a wire to the rubber surface. It is advisable to protect the bearing parts to avoid damages.
- When using hoist equipment, be careful of lubricating oil flying off onto a rubber roller surface. In case it happens, wipe it off immediately.
Instruction for storage
- When storing a rubber roller, hold at the shafts or stand the roller upright.
- Rubber rollers should be stored at cool and dark places. Do not store them near electrical equipment such as a motor and a germicidal lamp which generate ozone.
- We recommend re-polishing rollers which have been stored for more than 6 months. Wrapping the rubber roller surface with paper will slow down the surface oxidation.
- For large and heavy rollers with soft rubber material, rotate the rollers at regular intervals to avoid curving or bending.
Instruction for use
-
1. Pressure and speed
In general, the maximum load capability on a rubber roller is 100 kgf/cm in linear pressure but it varies greatly depending on the rotation speed, the rubber materials, the rubber hardness, the rubber thickness, the temperature, the iron core construction, the chemicals and so on.
Depending on the operating condition, the maximum load capability can be designed for more than 100 kgf/cm. If a roller is used at high speed and/or with large load, we recommend a roller core with a structure which can be water cooled so that water cooling can remove heat, so called hysteresis heat, which is generated when a rubber is being nipped. -
2. Temperature
Avoid rapid heating.
The maximum highest temperature for use of each rubber material are shown oncharacteristics of each rubber gradebut heat resistance of the adhesive layer is lower than rubber material’s. If a roller is used under high temperature, the roller should be cooled down from inward of the roller core. -
3. Chemicals
The chemical properties of each rubber material for the most part are shown oncharacteristics of each rubber gradeIf a roller is used in a special condition, please supply us the chemicals in use so that Katsura will select the suitable rubber material.
-
4. Mechanical Factors
Wear-out of a bearing, an axis and a gear, unfair loading and machine shaking cause over wear-out of a rubber surface or shortening of a roller life time.
Care should be taken for these factors. The same care should be taken for an unbalanced roller or a deflected roller.
- What is RUBBER ROLLER
- About Special Surface Finish